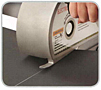
Electric Conveyor Belt Cutter
(2) Safe, Power Assisted Belt Cutting For Rubber Belts Up To 2" (50 mm) ThickThe Electric Belt Cutter from Flexco quickly and easily cuts all types of belting from the softest of natural rubbers to the hardest constructed solid woven PVC and fabric plied belts. Complimenting the existing range of Flexco belt cutters, the Electric Belt Cutter is safe and easy to use.
- Available in two sizes. The EBC1 allows for cuts up to 1" (25 mm) thick on rubber belts and up to a maximum 360 P.I.W. (630 N/m) on PVC belts. The EBC2 provides for a thicker cut up to 2" (50 mm) on rubber belts and up to a maximum 1140 P.I.W. (2000 N/m) on PVC belts.
- Designed for cutting all belt widths as well as for extended, longitudinal cuts.
- High speed, steel blade provides for a smooth, accurate cut and is protected by a spring loaded blade guard for enhanced worker safety.
- Sealed ball bearings support the belt during cutting and allow the operator to feed the cutter into the belt with minimal effort.
- Constructed of special high speed steel, the Electric Belt Cutter blade is dual angled for smooth, accurate cutting.
- Side handle can be mounted on either side for left or right hand operation.
- Spring loaded blade guard protects operator from cutting edge of blade.
- Top mounted eye bolt for attaching cutter to tool balancer.
- Permanently sealed gearbox provides long lasting, maintenance free operation.
Electric Belt Cutter
Designed for fast, accurate cutting, the Electric Belt Cutter is powered by a hammer drill. The heavy-duty stainless steel housing construction is strong, durable, and corrosion free and the permanently sealed gearbox provides for long lasting, maintenance free operation. The Electric Belt Cutter can be easily adapted for either right or left hand operation.
The Electric Belt Cutter is packaged in a durable, protective carrying case. Each complete unit includes an EBC1 or EBC2 Electric Belt Cutter with attached hammer drill and power cord, handle, and instruction guide. /Asset/a4685.jpg
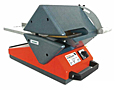
Novitool® Ply 130™ Ply Separator
(14) Easy Splitting of Conveyor BeltsThe Ply 130™ is used to separate between the plies of a conveyor belt. This cutting action is often required in preparation before splicing a belt with a splice press. A great advantage of this ply separator is that it can split as deep as 5" (130 mm) in one action. This is especially helpful when splitting very thin belts or belts where the material is difficult to cut, like with thin polyurethane belts. There are 2 models - one for workbench use (PLY 130 WB) and one with a stand (PLY 130 SA).
Capable of Splitting a Variety of Thermoplastic Belts
The robust construction of the Ply 130™ allows for precise splitting of thermoplastic belts - both thin and thick. As little as 0.02" (0.5 mm) can be separated - allowing for users to create film from the belt used in the vulcanizing process.
Easy Operation - One handle determines the splitting position.
Easy Depth Adjustment - Adjustable guide with ruler.
Excellent Repeatability - Achieve perfect results time after time.
Robust Machinery - Durable components and construction.
Easy operation - Multiple separations
The Ply 130™ can be used to prepare finger over linger splices and stepped splices. With only one handle you determine the depth you want to split the belt. It is possible to split between every layer of the belt and in this way generate two or three separations within one belt. /Asset/a4697.jpg
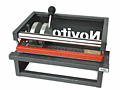
Novitool® Pun M™ Mobile Finger Punch
(3) Prepare Finger or Finger-Over-Finger SplicesThe Pun M™ is designed to effortlessly punch fingers into polyurethane and PVC conveyor belts in preparation for installing vulcanized splices. The tool is available in 3 standard widths; 12" (300 mm), 24" (600 mm) and 36" (900 mm). The open construction of the punch enables punching wider belts in multiple steps.
Ideal for Working on Location
The Pun M is manually operated and does not need electricity or air pressure for its operation. The punching force of 11,000 lbs. (50 kN) is created by pulling the lever and is easily done with one hand by an average person. Because of its easy set-up and manual operation, the Pun M is an ideal tool for working on location, as well as in a workshop.
Easy Operation - One hand clamping bar.
Flexible Configurations - For all types of finger punching.
Manually Operated - No electricity or air pressure needed.
Portable Equipment - For on-site use.
Easy Operation
To punch a belt, one belt end is positioned against the end stop and then clamped in place. Precise fingers are quickly punched with each lever pull.
Punch Types
Depending on the desired finger dimensions, Flexco offers a variety of punchboards for the Novitool Pun M™ Please note that punchboards are supplied separately. When ordering a new tool please state the desired punchboard (s). /Asset/a4691.jpg
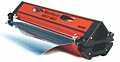
Novitool® Portable Splice Press
(5)The All In One Splice Press
The Aero™ Press is revolutionizing the splicing industry due to its ease of use and quick cycle time. This air cooled press has all components integrated into the tool, allowing a user to simply plug it into electricity and it is ready for use.
Efficient & Fast Splicing - All In One.
Once taken from the flight case the unit is fully operational and ready to splice. There are no external systems such as water tanks and pumps needed. All functions and subsystems are integrated into the press. The press has an integrated air-cooling system which ensures that the belt is quickly cooled down. This increases the splice quality and the operating speed of the press. For most belt materials, the entire operation can be completed within 7 to 12 minutes. This means a minimum interruption of the processes in which the conveyor bells are used.
Less Downtime - Splice in 7-12 minutes.
All-In-One Unit - No external components.
Integrated Air Cooling - No water required.
Portable Equipment - Flight case included.
Aero™ Specifications
The Aero™ splice press is available in five different models ranging in width from 24" (300 mm) to 60" (1500 mm). The unit operates on most common voltages. The Aero™ splice press can be used for splicing PVC and polyurethane belt materials ranging in width from 1/2 - 60" (10 to 1524 mm) depending on the model.
Easy to operate and excellent splice repeatability
The Aero™ has two controllers. One for adjustment of temperature and time and one for setting the pressure generated by the built-in compressor. The material / splice specific pressure and temperature values are easily set and the splicing operation itself is fully automatic. The temperature controller has a scrolling display which navigates the user through the settings in clear text messages.
With two quick-clamping bars it is easy to position and fasten the material in the press. The clamping bars ensure that the material remains in position during the entire splicing process.
Temperature control and cooling
With the Aero™ press, the user can set different splice temperatures for the upper and lower plate or use a single temperature for both platens. This function makes it easy to obtain even better splice results for belt materials with a fabric inlay or coating.
Unique programming features enable a more precise setting of the dwell time (down to seconds), an automatic dwell time countdown and a preheating cycle. A controlled - stepped - preheating will provide better splice results with thicker or less heat conducting belt materials.
The splice platens have integrated cool zones on both sides of the heating zone, This will result in ultra smooth splices even for the most difficult belt materials. No inlays of glass fibre or stainless steel are used which may cause pressure differences. The applied pressure will be the same at any point of the splicing plate. This design results in:
- No sinking of the hot splice plates into the molten belt material
- No bumps next to the splice
- Less shrinkage of the fingers
- Diminished shiny lines
With conventional systems these malformations are often difficult to control and will require possible process adjustments, trial runs and a lot of craftsmanship. However, the Aero™ can be operated with minimal training. With the right predefined settings the unit generates repeatable, high quality splices time after time.

Smartclamp™ Belt Clamps
A Complete System to Work Safer and SmarterAs part of Flexco Safe™ belt conveyor maintenance solutions, the SmartClamp™ system provides both safety and efficiency when clamping belts for installation of Clipper® and Alligator® mechanical belt fasteners.
Safer.
The SmartClamp™ was engineered to maximize strength and performance. The wedge grip design places an evenly distributed pressure load over the entire clamp interface. The set of four clamps permits safe pulling of belts with up to 2,000 lbs. (900 kg) of take-up load. Each individual clamp is rated up to a 1,000 lbs. (450 kg) load.
Faster.
Unlike other clamp systems which require time-consuming adjustments, the SmartClamp™ needs only a quick tap of a hammer to prelock the wedges. Attach and lighten come-alongs and the final lock is engaged. This fast setup saves precious and costly time during a breakdown situation.
With SmartClamp™ you do not need to sacrifice efficiencies for safety. These easy-to-install belt clamps make the choice obvious for maximum belt conveyor uptime.
Smarter.
Patent Pending /Asset/a4707.jpg
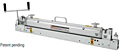
900 Series® Belt Cutter
(8) Designed to enhance operator safety with the fully enclosed cutting blade, this lightweight, portable belt cutter delivers straight, accurate cuts, time after time.These cutters are suitable for cutting belts up to 1.5" (38 mm).
Patent Pending /Asset/Flexco.jpg
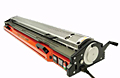
Novitool Amigo Splice Press, Cables and Templates for Monolithic Belts
Engineered for Precision Belt Splicing
Splices in monolithic belting must ensure tight pitch tolerance and be free from pinhole air pockets. Everything about the Amigo™ has
been designed to do just that. And in typical Novitool® design, it was made to do it with ease, safety, and speed.
Custom templates secure the belt when cut to ensure accurate pitch control. Then the contactless heating process splices the belt in less
than one minute and finishes with a controlled amount of clash. To ensure quality splices, pinholes are avoided through engineered
solutions such as the pre-heat function to remove moisture from the belt ends; the shielded heat zone for consistent heating in various
environmental conditions; and the contactless heating method. Accuracy, speed, and operator safety are fully integrated into the Amigo
design making it an ideal splicing tool for in-shop or on-site splicing.
- Integrated Belt Cutter maintains accurate pitch in a single pass
- Contactless Heating provides for a controlled amount of clash without actual contact with the heat source
- Shielded Heat Zone and Temperature control ensures splice parameter consistency regardless of ambient temperatures
- Operates on Single Phase 115V or 230V
- Digital Time Control with quick, simple splice settings; the Pre-Heat Setting can be used to remove moisture and avoid pinholes
- Interchangeable Splice Templates for precise pitch splicing of belts from various belt manufacturers